21 February 2024
Discover our technologies.
We regularly welcome interested customers to our technology centre and offer them the opportunity to see the performance of our CNC solutions for themselves on site and in person. In order to be able to present our latest technologies for more precise and efficient chipping processes, we have recently updated a large part of our exhibition.
Let us convince you of the performance and possibilities of our diverse solutions.
Milling technologies.
We are committed to the continuous further development of our products, always with the aim of fulfilling the needs and requirements of our customers. We want to provide you with solutions that not only enable maximum productivity, but also offer exceptional ease of use. As part of the latest updates to our technology centre, we are proud to present our latest innovations. Visitors will have the opportunity to experience 13 state-of-the-art machining centres in action and see for themselves their performance and efficiency live under chip removal.
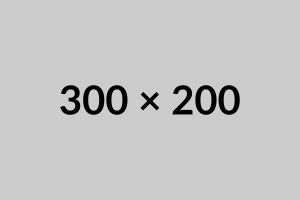
4/5-axis all-rounder for single parts and series in the smallest of spaces.
TILTENTA 7-2600 NEO: Whether end processing of long workpieces or 5-side complete processing - the TILTENTA 7 crossover concept releases many machining tasks in machine, tool and vehicle construction. The combination of a continuously swivelling main spindle and a long machine table with integrated NC rotary table allows the mixed production of single parts and series.
50kW powerhouse with SK50 for extreme requirements.
TILTENTA 10-3600: Full 5-axis machining up to 2,200 kg, vertical machining up to 6,200 mm, front side processing up to approx. 5,000 mm, oscillating machining, SK50 power - and all this with constant machine dynamics, regardless of the workpiece weight. Thanks to the travelling tool magazine, you as the user benefit from short chip-to-chip times over the entire travel path.
Milling technologies.
In combination with innovative automation systems.
Manufacture large, heavy workpieces automatically.
ACURA 85 + MARATHON SR518: With 18 pallets of 500 x 500 mm each, 700 mm interference circle and 470 kg transfer weight, the MARATHON SR518 multi-pallet magazine is designed for handling large, heavy single parts as repeat parts or small to medium series. Together with the powerful ACURA 85 5-axis machining centre, the optional 50 kW spindle and a 344-position STANDBY tool magazine, it forms a perfectly coordinated team for maximum productivity.
Entry-level automation solution with 6 pallet storage locations.
ACURA 65 + MARATHON PL406: The compact fixture storage unit with 6 pallet storage locations and a transfer weight of max. 370 kg enables you to achieve minimum tooling times for the subsequent order, even with mixed production of single parts or small to medium series. For easy operating, the pallet magazine has buttons for rotating the pallet carrier and for acknowledging raw parts.
Efficiency-enhancing set-up options.
Tooling optimisation is a crucial aspect that should definitely be taken into account when planning a new CNC machining centre. With our wide range of setup optimisation options, we design every machining centre to create a customised solution concept for our customers. Experience various highlights live in our technology centre.
Visit us.
Discover the top performance of our CNC technology up close: We cordially invite you to visit our technology centre in Meppen and see the precision of our machining centres for yourself. Arrange an individual demonstration appointment or register for our exclusive in-house exhibition.
We look forward to welcoming you and introducing you to our latest CNC technology.
Personal demonstration appointment.
Visit us in Meppen and see our CNC solutions for yourself. Gain an insight into our production processes and get to know the people behind the HEDELIUS brand. Experience various CNC machining centres live in action in our technology centre. Make an appointment with our expert advisors today!
More news.
HEDELIUS managing director Dennis Hempelmann presents the outstanding advantages of the FORTE 65 and FORTE 85 machining centres. Thanks to the Operator's platform design, you benefit from maximum dynamics, optimised chip fall and maximum ergonomics. With spacious tool magazines, innovative zero-point clamping technology and intelligent automation solutions, you can sustainably increase your productivity. Experience precision and efficiency at a new level!
How is HEDELIUS meeting the current challenges in European machine tool manufacturing? What role does automation play in this - and what can the industry expect in the future? In this interview, Dennis Hempelmann provides insights into the strategic direction, new machine concepts and the importance of innovation in turbulent times.
Our latest innovation in the video: The TILTENTA 7 NEO, automated with the MARATHON SR415! Experience how our managing director Dennis Hempelmann presents the advantages of this 5-axis universal machining centre with multi-pallet magazine. See for yourself how unutilised potential can be tapped and production processes opened up to a new level of efficiency.